- September 20, 2023
- Perspectives
Horizontal Directional Drilling: Navigating the Path to Efficient Infrastructure Installation
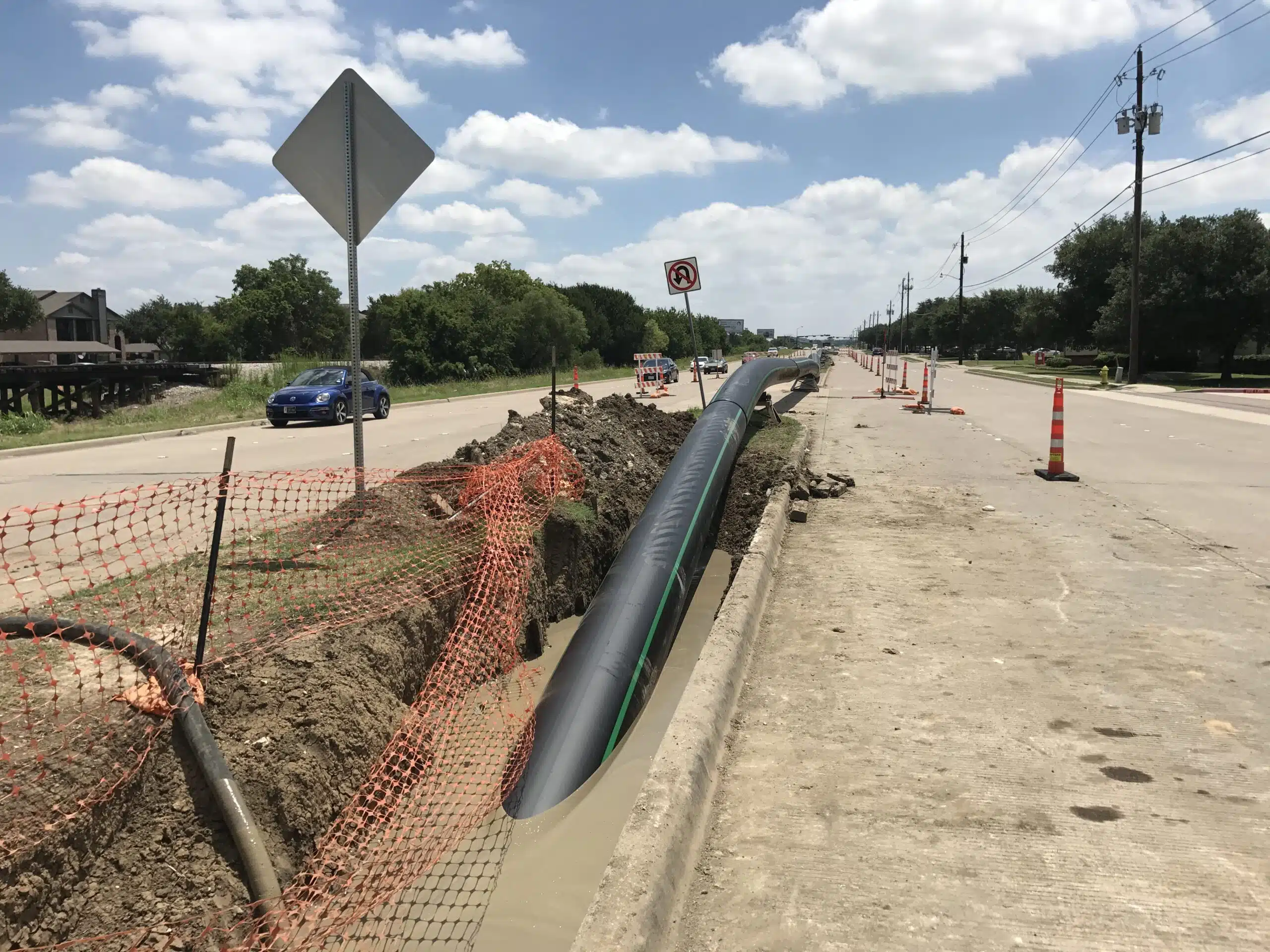
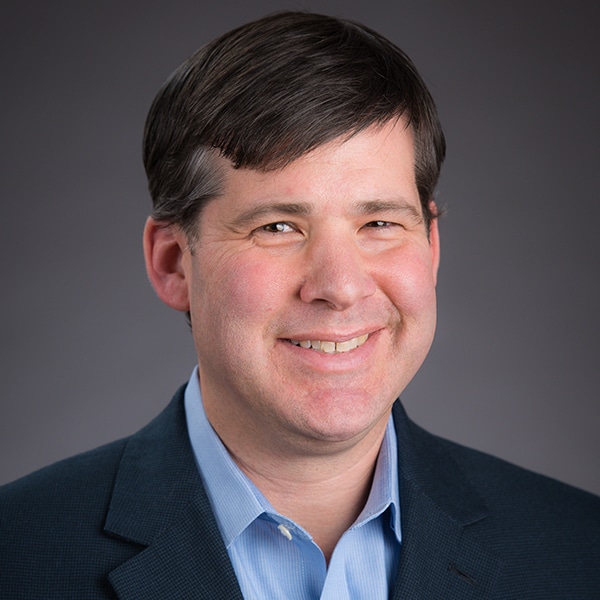
Scott Funk,
PE, ENV SP
Trenchless Technology Project Manager
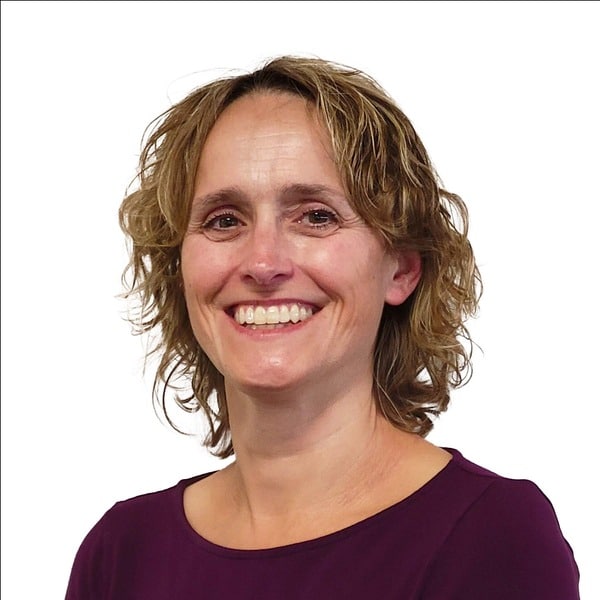
Deanna Martin, PE
Trenchless Technology Engineer
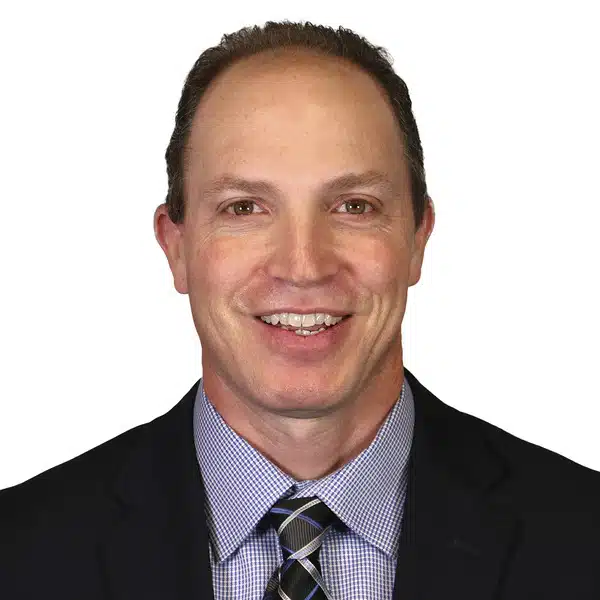
Marty Paris, PE
Trenchless Technology Practice Leader
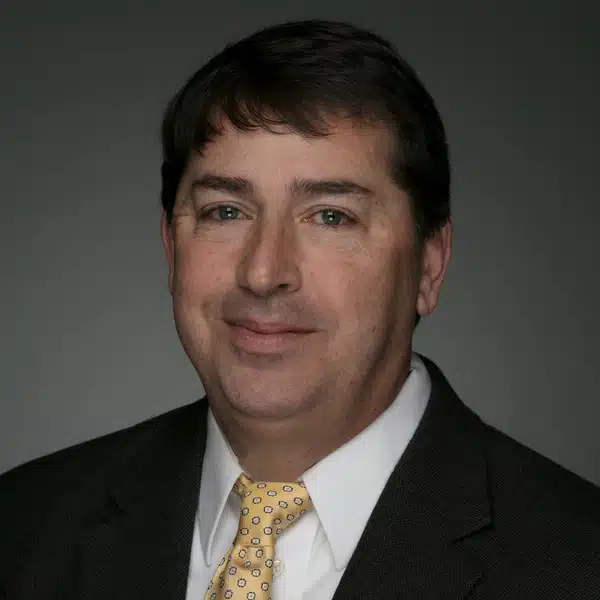
Charles Starling, PE, BCEE
Trenchless Technology Engineer
In modern infrastructure development, innovative techniques are revolutionizing underground utility installation. One of these techniques is Horizontal Directional Drilling (HDD)—a trenchless method of installing underground utilities and pipelines that helps us lay the foundations for our urban landscapes and strike a balance between progress and preservation. In this article, we answer some key questions about HDD, uncovering its capabilities, benefits, limitations, and the exciting horizons it continues to unveil.
What is Horizontal Directional Drilling?
Horizontal Directional Drilling is a trenchless approach to underground utility, cable, and pipeline installation. HDD uses a steerable surface-launched directional drilling machine to accurately drill along a chosen path to create a small diameter initial pilot hole. The opening is widened to pull the pipe through the hole, resulting in a continuous segment of the conveyance line.
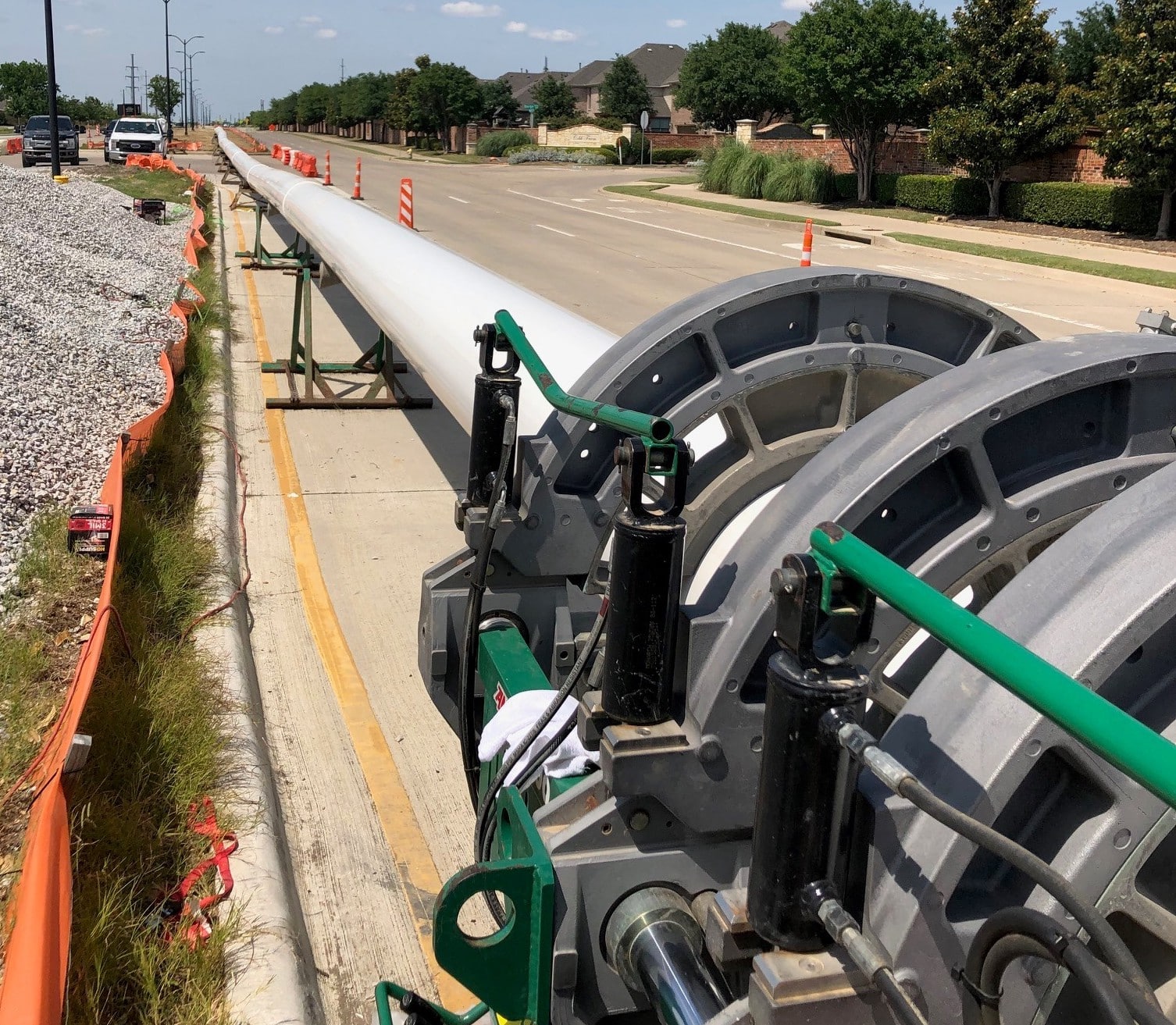
What Are the Benefits of Horizontal Directional Drilling?
Diverse Infrastructure Projects
A wide range of infrastructure projects—such as installing telecommunications, gas, water, and sewer pipelines or electrical conduits and fiber-optic cables—utilize HDD. It is one of the most common methods for installing small diameter telecom and gas conduits using high density polyethylene pipes. HDD is a great option for installation lengths between 300-500 feet, but lengths up to 10,000 feet have been completed.
Minimal Disruption to the Environment
HDD causes minimal surface disruption, which minimizes the impact of construction activities on the local environment and surrounding community, including residents and businesses. There’s also a decreased risk for soil erosion, sedimentation, and the release of pollutants into the environment.
Efficient Installation
Since HDD eliminates the need for large trenches, installation times are faster than traditional excavation methods. It is also a more efficient way to install pipelines and utilities in various soil types and locations—including under rivers, highways, and other obstacles.
An example of horizontal directional drilling. Kimley-Horn provided engineering services for the HDD of 1,935 feet of 20 inch DR18 Fusible PVC on the Legacy South Force Main – City of Frisco, Texas project.
What Are the Drawbacks of Horizontal Directional Drilling?
Land Conditions Must be Known
HDD requires complete information about the surrounding environment and underground conditions to ensure the chosen alignment will not damage existing utilities. Another requisite for HDD is access to both the start and end points of the borehole, which can be challenging if the weight and size of the equipment exceeds the size of the site. In these cases, traditional excavation methods or other trenchless technologies are more effective.
Installation Requirements and Costs
HDD is cost-effective when compared to traditional excavation methods for large-scale projects, but due to the specialized equipment and the expertise needed to operate it, HDD can cost more for small-scale projects.
HDD serves smaller-diameter utilities and pipelines well, and sizes from 24-48 inches are becoming more common, with some installations up to 60 inches in diameter. For larger-diameter projects, other excavation methods may be more appropriate.
Horizontal directional drilling requires drilling fluids to flush the hole before the pipe is pulled through, requiring additional space (around 25% more). This extra room is not always available with lines crossing under roadways or other existing infrastructure. Another concern with drilling fluids is the potential for an inadvertent return or surface release of drilling fluids in areas with shallow cover.
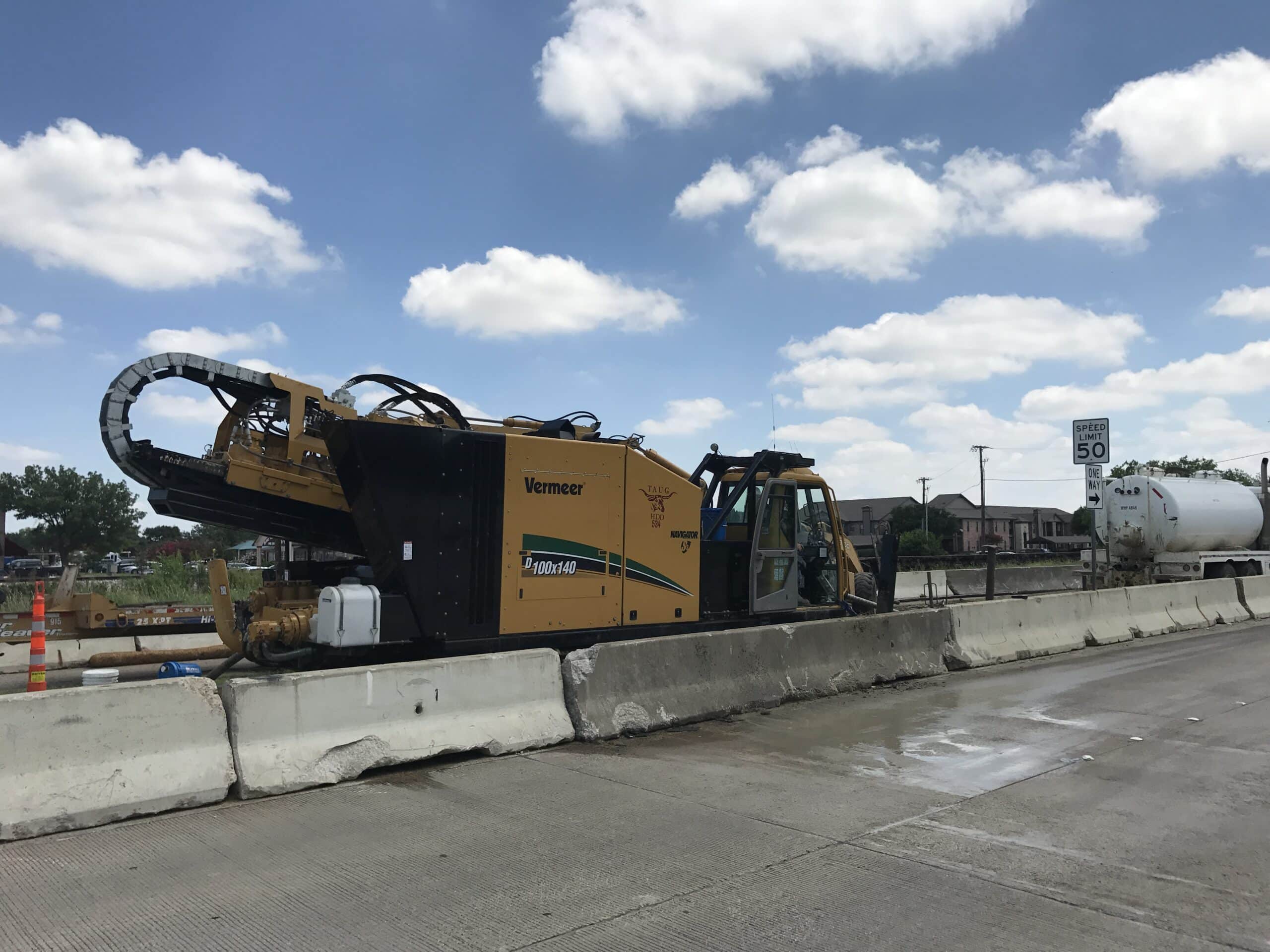
What is the Future of Trenchless Drilling?
HDD technology continues to evolve, and several improvements are in the works—including precision improvements of gravity pipeline installation that have better steering and tracking capabilities and more minor back-reaming criteria. We are also seeing the emergence of larger drilling rigs with the power to install pipelines of up to 25,000 feet in length.
At the same time, there’s a parallel trend toward developing even smaller rigs tailored to operate within constrained and confined areas. Finally, polymer gels are being integrated into the drilling process, reducing the reliance on bentonite slurry as a drilling fluid for a more efficient and environmentally conscious solution.
We’ve found HDD technology is an efficient, durable, flexible, cost-effective, and environmentally friendly underground utility installation solution that is changing the infrastructure development industry for the better. Contact us to learn more about this trenchless technology alternative and get your HDD initiatives in the ground!
About the Authors
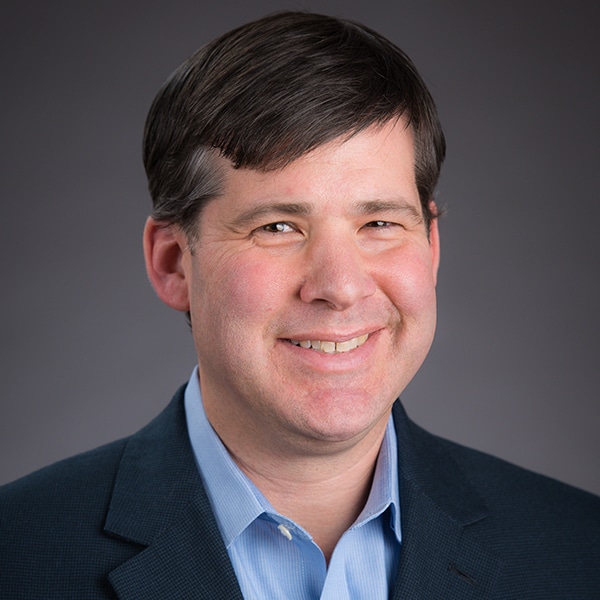
Scott Funk, PE, ENV SP
Scott offers more than 25 years of engineering experience, primarily involving the planning, inspection, evaluation, and rehabilitation and replacement design of water/wastewater collection and transmission system infrastructure. His experience includes trenchless and conventional open-cut utility construction of pipelines up to 84 inches in diameter as well as pump station design. Since 2005, Scott has managed the design and construction of infrastructure projects with an estimated construction value of $120 million.
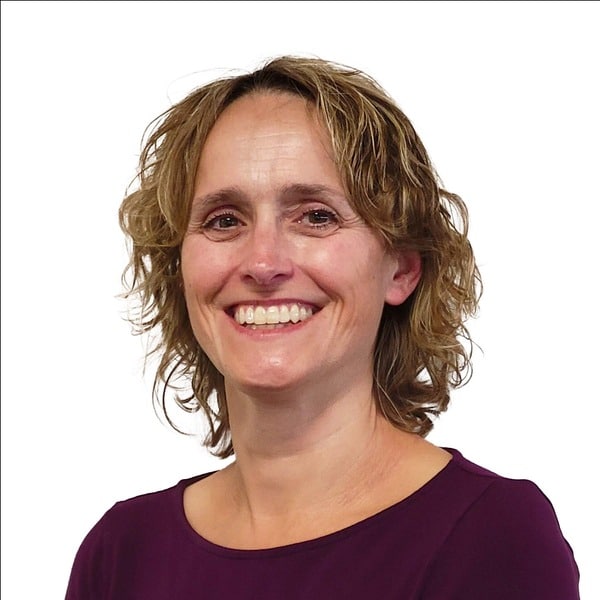
Deanna Martin, PE
Deanna has more than 20 years of experience in public works projects encompassing water/wastewater, utilities, pedestrian improvements, ADA-compliance improvements, roadway design, construction management, and field inspections. With a keen focus on leaving communities better than she found them, Deanna has improved critical Puget Sound systems by serving public agencies across Washington. Deanna brings experience managing projects with local, state, and federal grant funding programs. She takes pride in helping clients both enjoy and efficiently execute their projects.
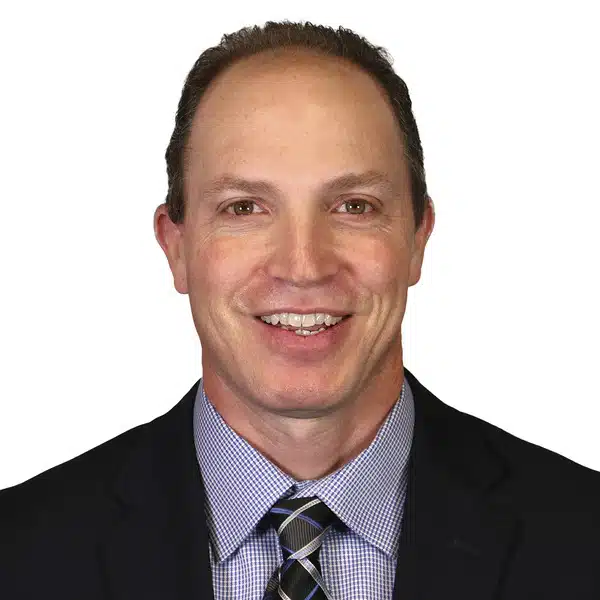
Marty Paris, PE
Marty is a Trenchless Technology Practice Leader with more than 30 years of experience in the design of water and wastewater infrastructure and rehabilitation projects. He has worked on over 200 miles of large- and small-diameter water and wastewater pipeline projects ranging from 6-inch to 120-inch and has assisted multiple municipalities with planning, design, and construction phases. He understands all project challenges and issues, ranging from the operations level to the administrative level. His experience includes 200,000 linear feet of trenchless replacement/rehabilitation methods, including cured-in-place, pipe bursting, horizontal directional drilling, microtunneling, fold and form, slip lining, tunneling, and horizontal auger boring.
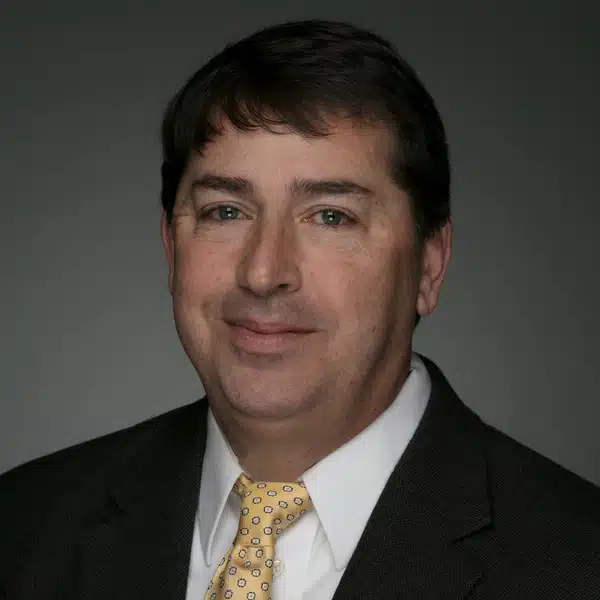
Charles Starling, PE, BCEE
With more than 25 years of experience as a project engineer and project manager, Charles works on a variety of utility engineering projects, including pump station design, force main design, condition assessment programs, and pump station assessment and rehabilitation. Charles utilizes his years of experience in project design, quality assurance, and project execution to provide quality client services on over nine FEMA projects. A Board-Certified Environmental Engineer, Charles also maintains professional engineering distinction in Alabama, Mississippi, Florida, and Louisiana.