- June 1, 2023
- Perspectives
Economic Resilience and Industrial Trends from NAIOP I.CON West
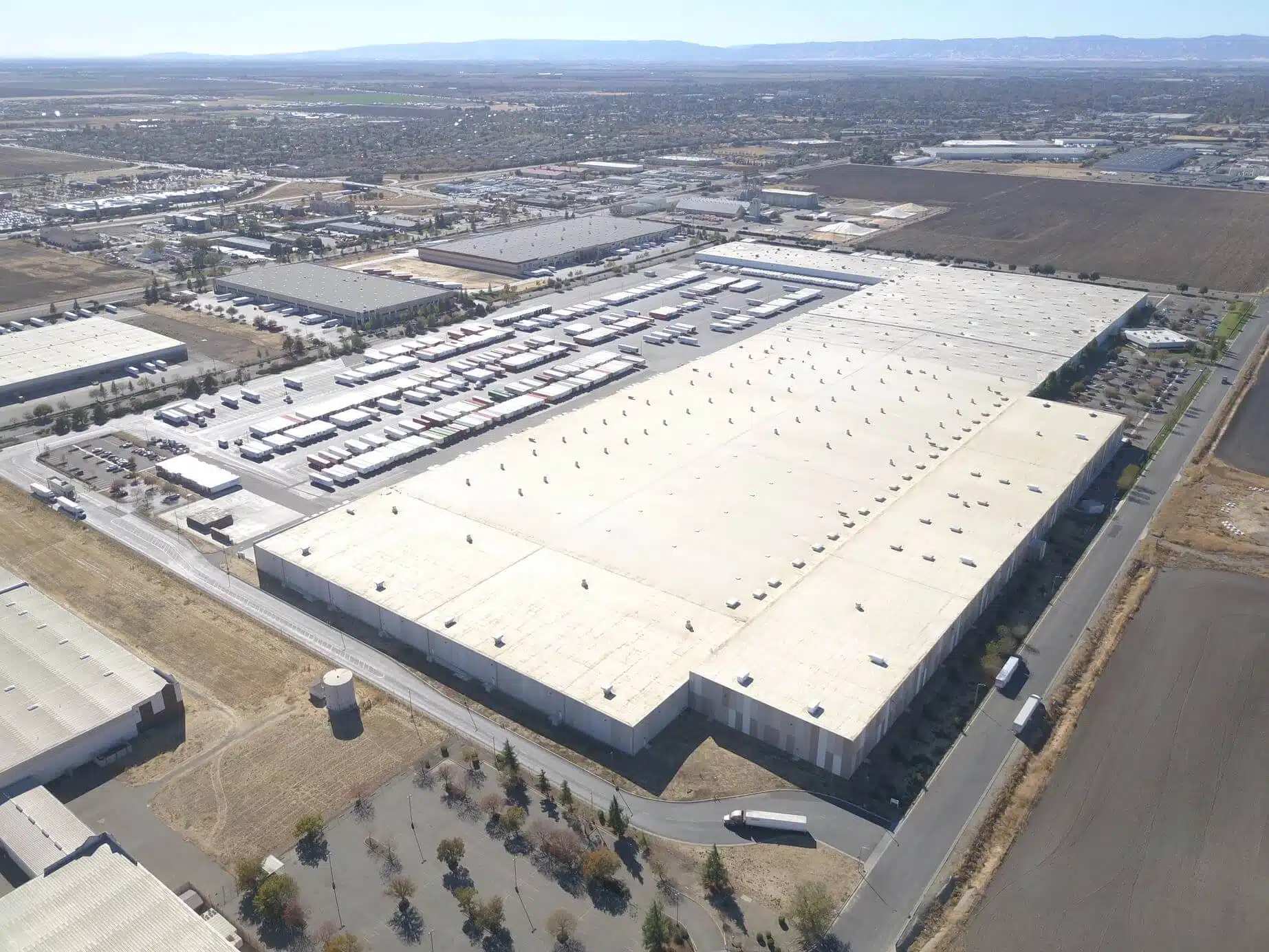
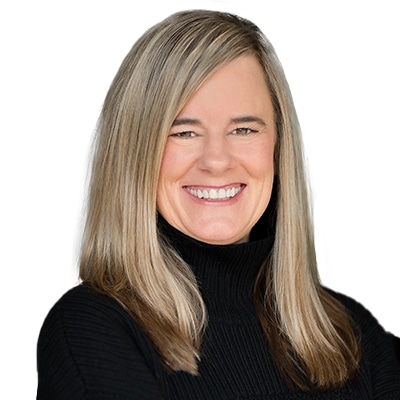
Jody Walker Belsick, P.E., LEED AP
Civil Engineer
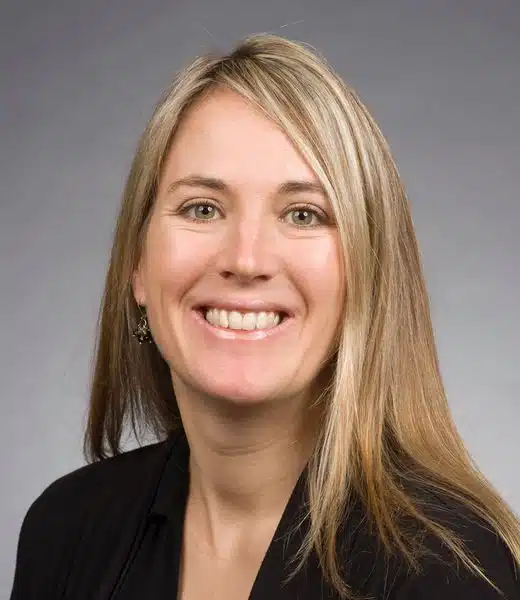
Jennifer Harry, P.E., LEED AP
Civil Engineer/Entitlement Lead
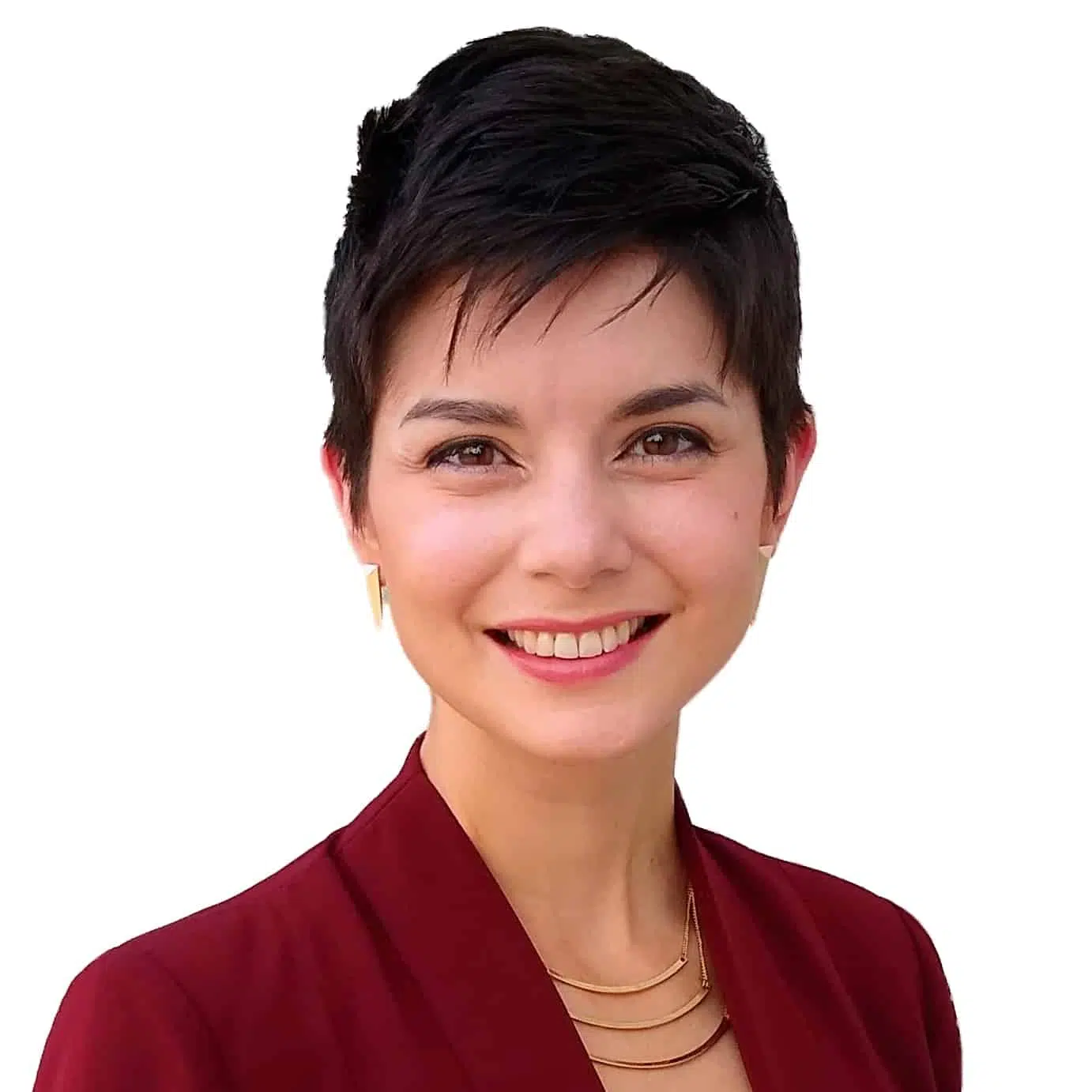
Marianna Hunnicutt, P.E., ENV SP
Civil Engineer
In the wake of increasing interest rates, inflation, and oncoming recession concerns, this year’s National Association of Industrial and Office Properties (NAIOP) I.CON West conference focused on economic projections, industry resilience strategies, engaging with industrial development peers, and emerging market potential. We’ve compiled the main takeaways here and offer our perspective on the industrial sector’s trajectory in the next few years.
Industrial Sector Resilience in a Changing Economy
A key focal point of I.CON West was the mild recession on the horizon. Unprecedented interest rate hikes, rising wages, construction and material costs, inflation, and labor shortages are creating market instability and challenging underwriting and investing potential. Although economic recovery began in 2022, these unique economic conditions will likely continue impacting the industrial sector into early 2024.
Despite the economic challenges of 2023, the industrial sector is poised to remain resilient as demand for e-commerce remains high. For the next two years, the absorption rate for the industrial sector is expected to remain stable through the economic turmoil, and vacancy rates are estimated to increase from 3.3% to 6%, which is considered “normal” for a tight market. Our takeaway is that, despite current economic conditions, industrial remains a growing force in the economy.
Industrial Real Estate Labor Market
Rebecca Rockey, Economist and Global Head of Economic Analysis and Forecasting at Cushman & Wakefield, gave the 2023 I.CON West keynote address on economic forecasting for the industrial real estate industry. Rockey focused on the impacts of slowing population growth and upcoming workforce retirement, which created a tight labor market and necessitated greater technology developments to fill the gaps.
In the next 10 years, NAIOP details in “Industrial Real Estate and the Economy: Where are We Headed?” almost one-fourth of the workforce will reach retirement age, leaving an estimated 3.9 million worker deficiency. Additionally, with an unusually low 3.4% unemployment rate, wage growth is not keeping up with inflation mandates, and Rockey suggested a mild recession and higher unemployment rates could promote economic growth in 2024-2025—essentially, a necessary “reset.” The current labor gap relative to jobs available, two job openings for every unemployed person, is not sustainable long-term, but it is not clear even to the best economists what the eventual labor market outcomes will be.
The labor market imbalance can be addressed in the meantime with technological advancement, such as robotics, artificial intelligence, manufacturing, and increased emphasis on trade apprenticeships and training. Additionally, emerging industrial trends—like multi-level warehouse structures, increased clear heights, superflat slabs, and improved operations and program efficiency—can also continue to develop the industrial market. These solutions have great potential to supply the missing knowledge and production until the economy adjusts.
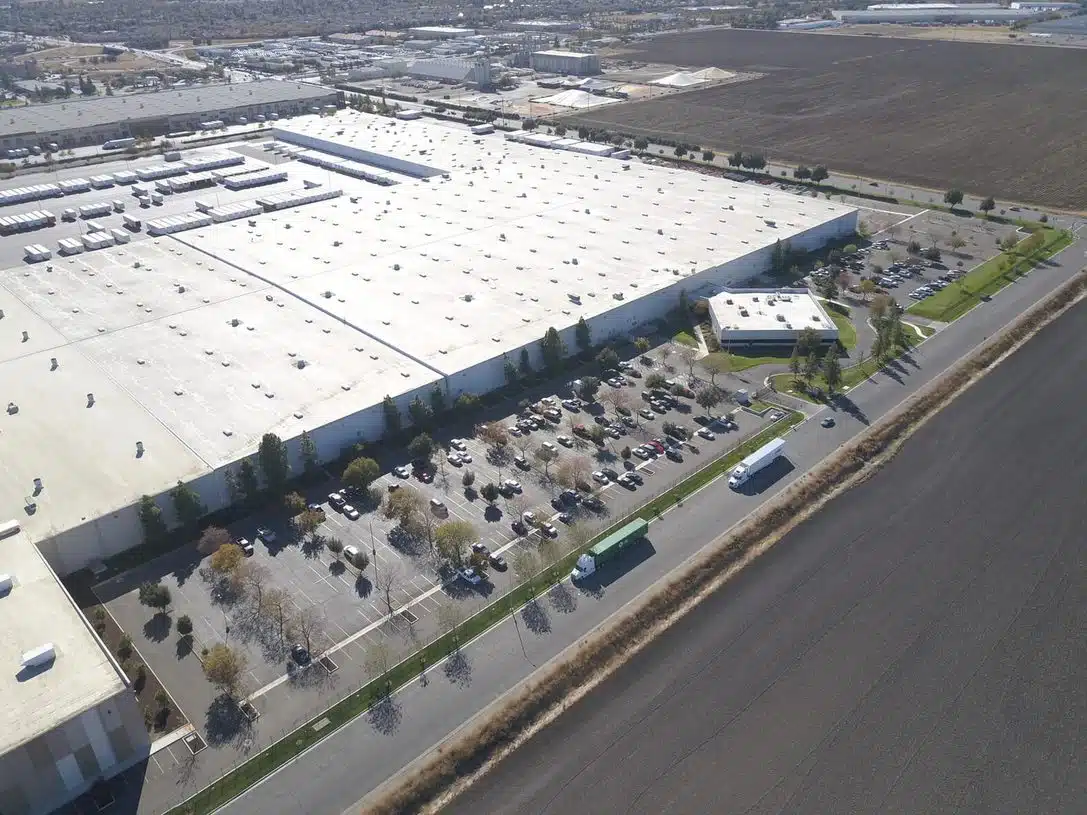
Emerging Industrial Trends
I.CON West detailed the lasting impacts of the COVID-19 pandemic on the industrial sector and the increasing complexity of industrial developments. Facilities are becoming larger, clear heights are increasing, nearshoring is impacting manufacturing expectations, and there is heightened interest in build-to-suit facilities and adaptive reuse of older buildings.
More specific design trends like clear heights, superflat slabs, and accommodation for robotics, manufacturing, and cold storage facilities are becoming popular in the post-pandemic industrial revolution. In fact, this year, there is an entire separate conference being offered by NAIOP focused on cold storage for the first time ever.
To meet the market’s demands, architects, engineers, and contractors must utilize creativity and approach design constraints with innovation, working with agencies to update and develop new standards, zoning codes, and design criteria as product types evolve.
Nearshoring and Friendshoring
The “The Nearshoring Experiment” session focused on how economic and supply chain disruptions spurred by the pandemic provoked interest in nearshoring and friendshoring, which makes the United States or other nearby countries a foundational manufacturing base after the over-reliance on geographically distant manufacturing. For instance, Taiwanese Semiconductor Manufacturing Co. invested $40 million into the construction of two manufacturing facilities in Phoenix as part of its nearshoring friendshoring efforts.
Along with the growing prioritization of Eastern and Southern coast imports, Mexico is a key target for nearshoring efforts due to its low labor costs, delivery timelines, and reputation for producing high-value goods, including microchips and appliances. However, site constraints, geopolitical challenges, energy requirements, and logistics encumber manufacturing and importing from Mexico, but increasing rail access across the Texas-Mexico border could alleviate some of these concerns while maximizing nearshoring benefits.
Cold Storage
Cold storage facilities were a conference hot topic and are explored in “Cold Storage: Demand, Design, and Drivers,” and this growing industrial market has been largely driven by the economic boom in e-commerce and grocery delivery services during COVID. These facilities must be able to support varying product temperature needs—from food to medicine to chemicals—as well as the transportation of these products in quality condition.
In 2022, the U.S. cold storage warehousing and distribution market was valued at more than $35 billion, and it is only expected to increase in the upcoming years. Almost 80% of current structures have existed for more than two decades, requiring both the construction of new facilities to accommodate growth trends and the upgrading of older facilities to integrate automated systems and robotics to offset a workforce shortage.
Adaptive Reuse for Affordable Housing
According to “Adaptive Reuse,” after COVID-19 and work-from-home priorities upended the office market, related office vacancies increased to a national rate of more than 17% in 2022. Companies searching for industrial space have not been as interested in adapting these vacant, older office buildings, instead seeking sophisticated structures with greater clearances, more space, specific racking and bay design criteria, and provision for technological upgrades like robotics. This has created a growing number of older industrial buildings that are still in good condition but are unused.
Simultaneously, almost a quarter of American renters spend half or more of their income on rent costs that continue to rise, and adaptive reuse of empty industrial buildings has become an attractive option to both solve affordable housing deficits and revitalize older, vacant structures. If the federal government incentivizes adaptive reuse, the conversion of these industrial spaces to housing units could not only be cost-effective, but could also promote sustainability and job growth goals in the unique post-pandemic industrial sphere.
Affordable housing has been one of the most-talked about needs at this conference and other CRE conferences that we have recently attended. There is a trend for adaptive reuse and motivation to pursue it; however, the financial and political logistics of actually implementing it are complicated and may prohibit its rapid integration into development markets. For instance, California has passed legislation for adaptive reuse incentives, but there is still a long way to go to make this a reality.
Southwest Industrial Market Potential
During the pandemic, the Southwest market experienced a significant shift due to increased e-commerce demand and population growth. Significant immigration from California, the Midwest, Southeast, and Texas as well as investor interest—particularly institutional capital—contributed to this market growth and the increase of build-to-suit over spec facilities.
In the Southwest, the unprecedented boom in industrial development is driven by the region’s accessibility to Southern California ports, reduced bureaucratic obstacles, and optimal distribution to multiple markets. Las Vegas and Phoenix specifically sit at prime locations—with relatively short driving distances from the port cities of Long Beach and Los Angeles while still being centrally located to other major markets in Reno, Salt Lake City, and Denver. Because truck drivers are restricted to 14-hour shifts and 11-hour drive limits, Las Vegas drivers in particular can make the commute to the ports, deliver their product, and start the return all within a day.
As lease rates continue to rise and demand is projected to remain healthy, it is expected companies across the nation will expand their businesses to development-friendly Southwest markets. Notably, East Coast companies are beginning to build more hub facilities in the Southwest outside of California. To meet this demand while it still exists, Guy Martin, I.CON West panelist and President of Martin-Harris Construction, encouraged developers to start designs and construction as soon as possible before construction costs become more expensive. Engaging consultants and contractors early can help make sure costs are known going into the land deal, allowing for time to ensure there are not key costs that are not factored into the overall land and tenant agreement.
Looking Forward
This year’s I.CON West conference was one of the most highly attended in recent history—even pre-pandemic—and energy was in the air. Like many of NAIOP’s conferences and events, I.CON West provides perspectives we find invaluable to developing a big-picture view of the industry. Moving forward, here are three action steps we recommend to leverage the I.CON West takeaways for industrial market growth:
- Expand your expertise, education, and training in the design and delivery of complex facilities such as manufacturing, cold storage, and automatization facilities.
- Partner with NAIOP committees and local officials to stay up-to-date on information and trends and optimize new market opportunities to cultivate sustainable economies and communities.
- Stay involved in federal, state, and local legislation in your market related to key topics—including permit timing, urban growth boundaries, climate/regulatory policies, tax incentives for industrial developments, and adaptive reuse—and leverage your NAIOP partners to help lobby where needed.
About the Experts
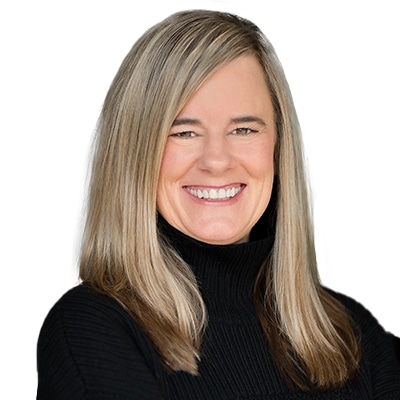
Jody Belsick, P.E., LEED AP
Jody has over two decades of civil engineering experience focused on development services, particularly specializing in industrial, sports, retail, and office developments in the western United States. The former owner of civil engineering firm Walker Engineering, LLC, Jody is now a member of Kimley-Horn’s Sports Task Force, and she collaborated closely with the Raiders on the impressive Henderson Headquarters and Allegiant Stadium as well as projects for Vegas Golden Knights, Formula 1, and AAA Baseball. Jody has also partnered with numerous retail and industrial clients—including Costco, Chick-Fil-A, and Prologis—to meet their development needs in a variety of geographic areas. Jody enjoys looking at project sites and solving complex development issues to provide the best project for the developers. Passionate about industrial real estate growth, Jody has held a variety of leadership positions at NAIOP and currently is a NAIOP Governor and a participant in the NAIOP National Forums. /telecommunications design, and electrical/communications utility coordination.
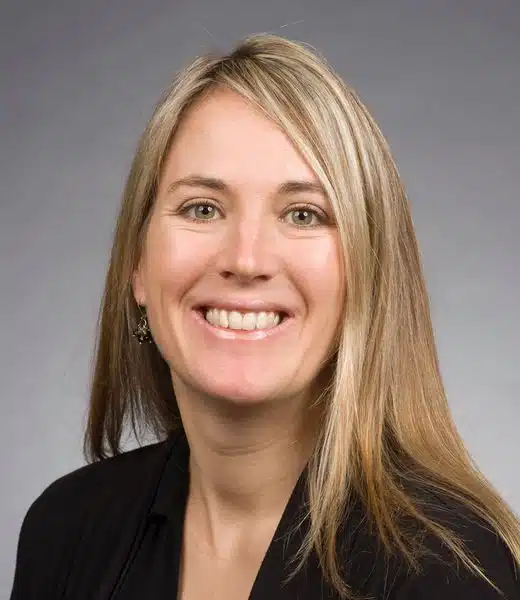
Jennifer Harry, P.E., LEED AP
With more than two decades of industry experience, Jennifer is an expert in private land development with a focus on entitlements and permitting. She is particularly focused on complex projects that require a development approach that is both innovative and solution-oriented. Integrating her background as a civil engineer with her planning experience on countless projects, Jennifer has the skill to navigate complicated entitlement processes in California and other challenging permitting environments. Passionate about all types of retail, industrial, and rail projects in a variety of geographic areas, she tends to follow her clients across city boundaries and state lines, leveraging Kimley-Horn's local office expertise to support each client’s unique development strategy and approach. Jennifer is currently working with NASCAR on their redevelopment of the Auto Club Speedway and also with Hillwood on the associated development of the Speedway Commerce Center II, a 6.6 million square foot high cube for logistics and e-commerce. In addition, she is leading entitlement and permitting efforts for BNSF’s 4,600 acre Barstow International Gateway Project in Barstow, CA.
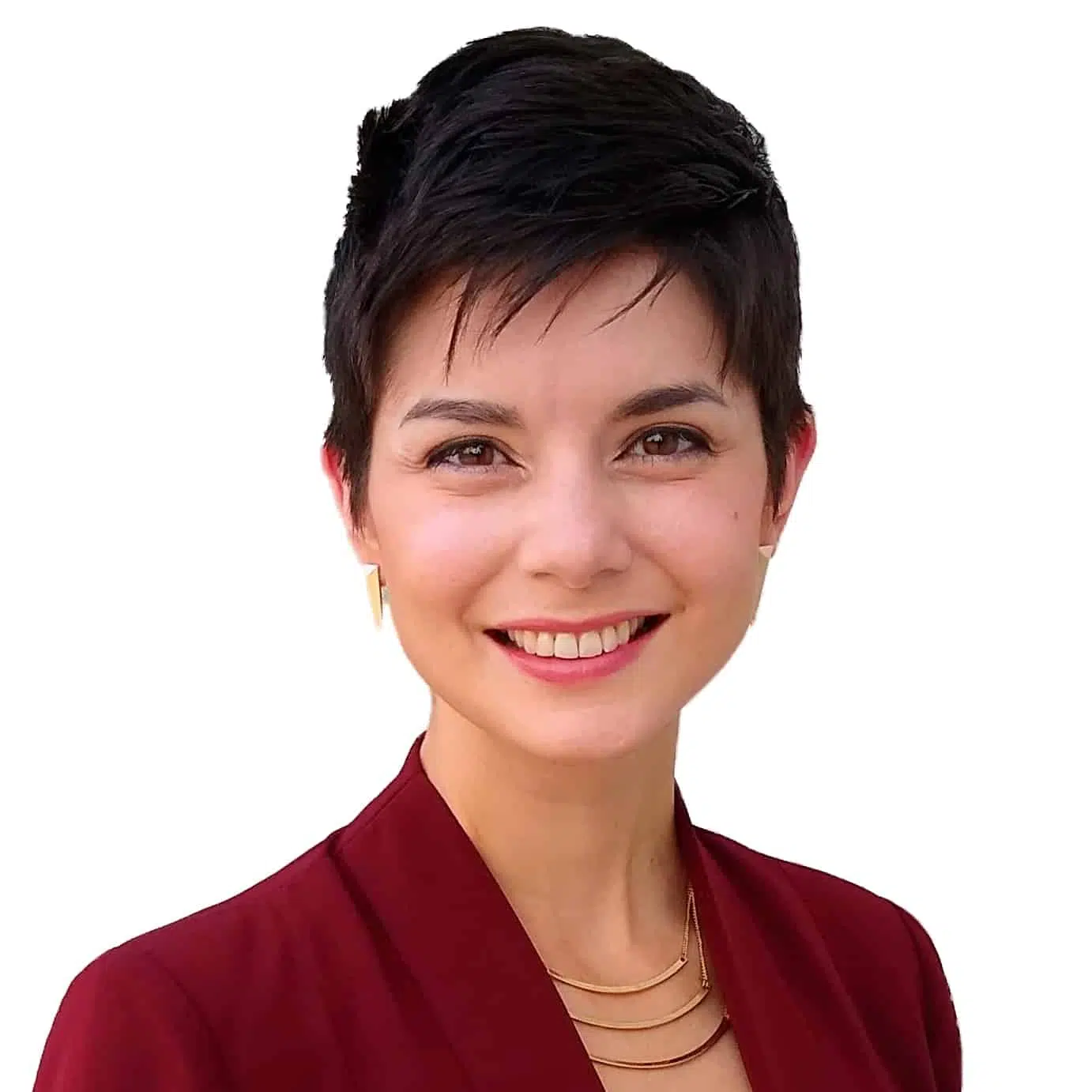
Marianna Hunnicutt, P.E., ENV SP
Marianna has more than a decade of experience in design and development services focused in industrial, retail, mixed-use, multi-family, office, military, sports, and entertainment venues. She has received recognitions at both the local and national stage for her efforts and contributions to the development community, including the 2022 Engineering-News Record Southwest Top Young Professionals, the 2021 NAIOP National Developing Leader of the Year, and the 2021 NAIOP Southern Nevada Chapter Developing Leader of the Year. Marianna also received the 2020 National NAIOP and Prologis Inclusion in CRE Scholarship for Women and Underrepresented Professionals. Marianna is a National NAIOP forum member representing the Southern Nevada market and a member of the NAIOP National Research Foundation Visionaries program.